Dankzij de snelle ontwikkeling van de nieuwe energie-industrie is laserlassen de afgelopen jaren snel doorgedrongen in de hele nieuwe energie-industrie vanwege de snelle en stabiele voordelen ervan. Onder hen is laserlasapparatuur verantwoordelijk voor het grootste deel van de toepassingen in de gehele nieuwe energie-industrie.
Laserlassenis snel de eerste keuze geworden in alle lagen van de bevolking vanwege de hoge snelheid, grote diepte en kleine vervorming. Van puntlassen tot stuiklassen, opbouw- en afdichtingslassen,laserlassenbiedt ongeëvenaarde precisie en controle. Het speelt een belangrijke rol in de industriële productie en productie, waaronder de militaire industrie, de medische zorg, de lucht- en ruimtevaart, 3C-auto-onderdelen, mechanisch plaatwerk, nieuwe energie en andere industrieën.
Vergeleken met andere lastechnologieën heeft laserlassen zijn unieke voor- en nadelen.
Voordeel:
1. Hoge snelheid, grote diepte en kleine vervorming.
2. Lassen kan worden uitgevoerd bij normale temperatuur of onder speciale omstandigheden, en de lasapparatuur is eenvoudig. Een laserstraal drijft bijvoorbeeld niet af in een elektromagnetisch veld. Lasers kunnen lassen in een vacuüm-, lucht- of bepaalde gasomgeving, en kunnen materialen lassen die door glas heen gaan of transparant zijn voor de laserstraal.
3. Het kan vuurvaste materialen zoals titanium en kwarts lassen, en kan ook ongelijksoortige materialen met goede resultaten lassen.
4. Nadat de laser is scherpgesteld, is de vermogensdichtheid hoog. De beeldverhouding kan 5:1 bereiken en kan oplopen tot 10:1 bij het lassen van apparaten met een hoog vermogen.
5. Microlassen kan worden uitgevoerd. Nadat de laserstraal is gefocusseerd, kan een klein plekje worden verkregen dat nauwkeurig kan worden gepositioneerd. Het kan worden toegepast bij het assembleren en lassen van micro- en kleine werkstukken om geautomatiseerde massaproductie te bereiken.
6. Het kan moeilijk bereikbare plaatsen lassen en contactloos lassen over lange afstanden uitvoeren, met grote flexibiliteit. Vooral de laatste jaren heeft de YAG-laserverwerkingstechnologie optische vezeltransmissietechnologie overgenomen, waardoor laserlastechnologie op grotere schaal kan worden gepromoot en toegepast.
7. De laserstraal kan eenvoudig in tijd en ruimte worden gesplitst, en meerdere stralen kunnen op meerdere locaties tegelijk worden verwerkt, wat de voorwaarden schept voor nauwkeuriger lassen.
Defect:
1. De montagenauwkeurigheid van het werkstuk moet hoog zijn en de positie van de balk op het werkstuk mag niet significant afwijken. Dit komt omdat de laserpuntgrootte na focussering klein is en de lasnaad smal is, waardoor het moeilijk is om vulmetaalmaterialen toe te voegen. Als de montagenauwkeurigheid van het werkstuk of de positioneringsnauwkeurigheid van de balk niet aan de eisen voldoet, kunnen lasfouten ontstaan.
2. De kosten van lasers en aanverwante systemen zijn hoog en de eenmalige investering is groot.
Veel voorkomende laserlasfoutenbij de productie van lithiumbatterijen
1. Porositeit van het lassen
Veelvoorkomende gebreken bijlaserlassenzijn poriën. Het lassmeltbad is diep en smal. Tijdens het laserlasproces dringt stikstof van buitenaf het gesmolten bad binnen. Tijdens het koel- en stollingsproces van het metaal neemt de oplosbaarheid van stikstof af naarmate de temperatuur daalt. Wanneer het gesmolten metaal afkoelt en begint te kristalliseren, zal de oplosbaarheid scherp en plotseling dalen. Op dit moment zal een grote hoeveelheid gas neerslaan en belletjes vormen. Als de zweefsnelheid van de bellen kleiner is dan de metaalkristallisatiesnelheid, zullen er poriën worden gegenereerd.
Bij toepassingen in de lithiumbatterij-industrie zien we vaak dat poriën vooral voorkomen tijdens het lassen van de positieve elektrode, maar zelden voorkomen tijdens het lassen van de negatieve elektrode. Dit komt omdat de positieve elektrode van aluminium is en de negatieve elektrode van koper. Tijdens het lassen is het vloeibare aluminium op het oppervlak gecondenseerd voordat het interne gas volledig overstroomt, waardoor wordt voorkomen dat het gas overstroomt en grote en kleine gaten vormt. Kleine huidmondjes.
Naast de hierboven genoemde oorzaken van poriën omvatten poriën ook buitenlucht, vocht, oppervlakteolie, enz. Bovendien zullen de richting en hoek van het uitblazen van stikstof ook de vorming van poriën beïnvloeden.
Hoe kan het optreden van lasporiën worden verminderd?
Eerst, vroegerlassen, de olievlekken en onzuiverheden op het oppervlak van de binnenkomende materialen moeten op tijd worden gereinigd; bij de productie van lithiumbatterijen is de inspectie van binnenkomend materiaal een essentieel proces.
Ten tweede moet de beschermgasstroom worden aangepast aan factoren zoals lassnelheid, vermogen, positie, enz., en mag deze niet te groot of te klein zijn. De druk van de beschermende mantel moet worden aangepast aan factoren zoals laservermogen en focuspositie, en mag niet te hoog of te laag zijn. De vorm van het mondstuk van de beschermende mantel moet worden aangepast aan de vorm, richting en andere factoren van de las, zodat de beschermende mantel het lasgebied gelijkmatig kan bedekken.
Ten derde, controleer de temperatuur, vochtigheid en stof in de lucht in de werkplaats. De omgevingstemperatuur en vochtigheid zullen het vochtgehalte op het oppervlak van het substraat en het beschermende gas beïnvloeden, wat op zijn beurt de vorming en ontsnapping van waterdamp in het gesmolten zwembad zal beïnvloeden. Als de omgevingstemperatuur en de luchtvochtigheid te hoog zijn, zal er te veel vocht op het oppervlak van het substraat en het beschermende gas aanwezig zijn, waardoor een grote hoeveelheid waterdamp ontstaat, waardoor poriën ontstaan. Als de omgevingstemperatuur en vochtigheid te laag zijn, zal er te weinig vocht op het oppervlak van het substraat en in het beschermgas aanwezig zijn, waardoor de vorming van waterdamp wordt verminderd, waardoor de poriën worden verkleind; laat het kwaliteitspersoneel de doelwaarde van temperatuur, vochtigheid en stof op het lasstation detecteren.
Ten vierde wordt de beam swing-methode gebruikt om poriën te verkleinen of te elimineren bij laserlassen met diepe penetratie. Door de toevoeging van schommelingen tijdens het lassen veroorzaakt de heen en weer gaande zwaai van de balk naar de lasnaad het herhaaldelijk opnieuw smelten van een deel van de lasnaad, waardoor de verblijftijd van het vloeibare metaal in het lasbad wordt verlengd. Tegelijkertijd verhoogt de afbuiging van de straal ook de warmte-inbreng per oppervlakte-eenheid. De diepte-breedteverhouding van de las wordt verminderd, wat bevorderlijk is voor het ontstaan van bellen, waardoor poriën worden geëlimineerd. Aan de andere kant zorgt de zwaai van de balk ervoor dat het kleine gat dienovereenkomstig zwaait, wat ook een roerkracht voor het lasbad kan opleveren, de convectie en het roeren van het lasbad kan vergroten en een gunstig effect kan hebben op het elimineren van de poriën.
Ten vijfde, de pulsfrequentie, de pulsfrequentie verwijst naar het aantal pulsen dat door de laserstraal per tijdseenheid wordt uitgezonden, wat de warmte-invoer en de warmteaccumulatie in het gesmolten zwembad zal beïnvloeden, en vervolgens het temperatuurveld en het stromingsveld in het gesmolten zwembad zal beïnvloeden. zwembad. Als de pulsfrequentie te hoog is, zal dit leiden tot overmatige warmte-inbreng in het gesmolten bad, waardoor de temperatuur van het gesmolten bad te hoog wordt, waardoor metaaldamp of andere elementen ontstaan die bij hoge temperaturen vluchtig zijn, waardoor poriën ontstaan. Als de pulsfrequentie te laag is, zal dit leiden tot onvoldoende warmteaccumulatie in het gesmolten bad, waardoor de temperatuur van het gesmolten zwembad te laag wordt, waardoor het oplossen en ontsnappen van gas wordt verminderd, wat resulteert in poriën. Over het algemeen moet de pulsfrequentie worden gekozen binnen een redelijk bereik, gebaseerd op de dikte van het substraat en het laservermogen, en voorkomen dat deze te hoog of te laag is.
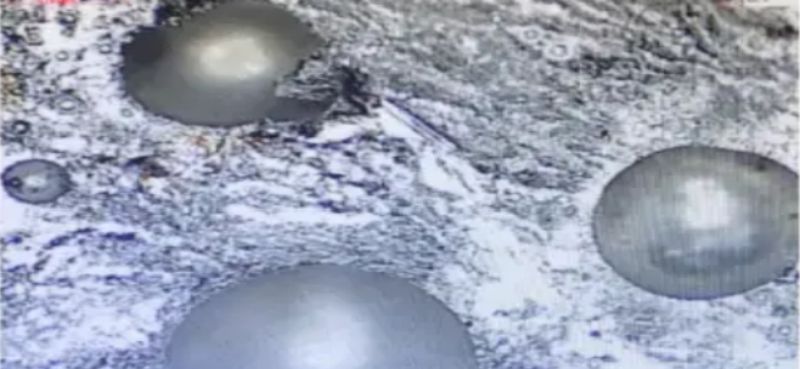
Gaten lassen (laserlassen)
2. Lasspatten
De spatten die ontstaan tijdens het lasproces en het laserlassen zullen de oppervlaktekwaliteit van de las ernstig aantasten en de lens vervuilen en beschadigen. De algemene prestatie is als volgt: nadat het laserlassen is voltooid, verschijnen er veel metaaldeeltjes op het oppervlak van het materiaal of werkstuk en hechten ze zich aan het oppervlak van het materiaal of werkstuk. De meest intuïtieve prestatie is dat bij het lassen in de modus van de galvanometer, na een periode van gebruik van de beschermende lens van de galvanometer, er dichte putjes op het oppervlak zullen verschijnen, en deze putjes worden veroorzaakt door lasspatten. Na een lange tijd is het gemakkelijk om het licht te blokkeren en zullen er problemen optreden met laslicht, wat resulteert in een reeks problemen zoals gebroken lassen en virtueel lassen.
Wat zijn de oorzaken van spatten?
Ten eerste de vermogensdichtheid: hoe groter de vermogensdichtheid, hoe gemakkelijker het is om spatten te genereren, en de spatten houden rechtstreeks verband met de vermogensdichtheid. Dit is een eeuwenoud probleem. Tot nu toe is de industrie er in ieder geval niet in geslaagd het probleem van spatten op te lossen, en kan alleen maar zeggen dat het probleem enigszins is verminderd. In de lithiumbatterij-industrie is spatten de grootste oorzaak van kortsluiting in de batterij, maar het is er niet in geslaagd de oorzaak ervan op te lossen. De impact van spatten op de batterij kan alleen worden verminderd vanuit het oogpunt van bescherming. Zo is er rond het lasdeel een cirkel van stofafvoerpoorten en beschermkappen toegevoegd, en zijn er rijen luchtmessen in cirkels toegevoegd om de inslag van spatten of zelfs schade aan de accu te voorkomen. Er kan worden gezegd dat het vernietigen van het milieu, de producten en componenten rond het lasstation de middelen heeft uitgeput.
Wat betreft het oplossen van het spatprobleem kan alleen maar worden gezegd dat het verminderen van de lasenergie helpt om spatten te verminderen. Het verlagen van de lassnelheid kan ook helpen als de penetratie onvoldoende is. Maar bij sommige speciale procesvereisten heeft het weinig effect. Het is hetzelfde proces, verschillende machines en verschillende partijen materialen hebben totaal verschillende laseffecten. Daarom is er in de nieuwe energie-industrie een ongeschreven regel: één set lasparameters voor één apparaat.
Ten tweede, als het oppervlak van het bewerkte materiaal of werkstuk niet wordt gereinigd, zullen olievlekken of verontreinigende stoffen ook ernstige spatten veroorzaken. Op dit moment is het het gemakkelijkst om het oppervlak van het verwerkte materiaal schoon te maken.
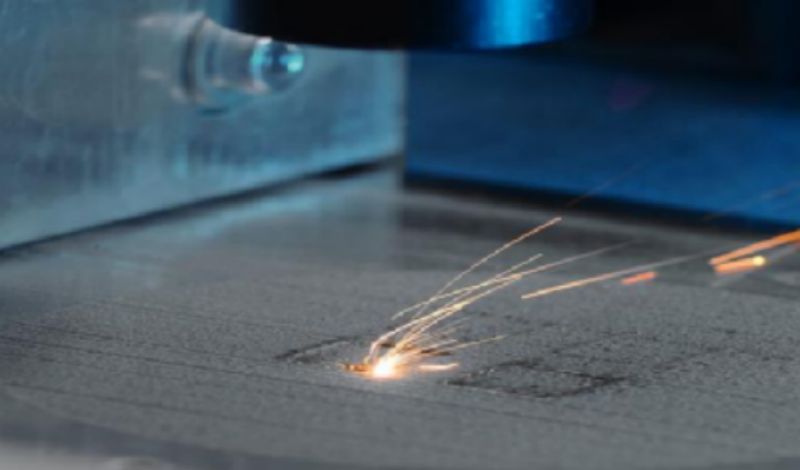
3. Hoge reflectiviteit van laserlassen
Over het algemeen verwijst hoge reflectie naar het feit dat het verwerkingsmateriaal een kleine soortelijke weerstand, een relatief glad oppervlak en een lage absorptiesnelheid heeft voor nabij-infraroodlasers, wat leidt tot een grote hoeveelheid laseremissie, en omdat de meeste lasers worden gebruikt verticaal Door het materiaal of een kleine helling komt het terugkerende laserlicht opnieuw de uitvoerkop binnen, en zelfs een deel van het terugkerende licht wordt gekoppeld in de energieoverbrengende vezel en wordt teruggestuurd langs de vezel naar binnen van de laser, waardoor de kerncomponenten in de laser blijven op hoge temperatuur.
Wanneer de reflectiviteit tijdens het laserlassen te hoog is, kunnen de volgende oplossingen worden gekozen:
3.1 Gebruik een antireflectiecoating of behandel het oppervlak van het materiaal: het coaten van het oppervlak van het lasmateriaal met een antireflectiecoating kan de reflectiviteit van de laser effectief verminderen. Deze coating is meestal een speciaal optisch materiaal met een laag reflectievermogen dat laserenergie absorbeert in plaats van terug te reflecteren. Bij sommige processen, zoals het lassen van stroomcollectoren, zachte verbindingen, enz., kan het oppervlak ook worden gebosseleerd.
3.2 Pas de lashoek aan: Door de lashoek aan te passen, kan de laserstraal onder een geschiktere hoek op het lasmateriaal invallen en het optreden van reflectie verminderen. Normaal gesproken is het een goede manier om reflecties te verminderen als de laserstraal loodrecht op het oppervlak van het te lassen materiaal valt.
3.3 Hulpabsorptiemiddel toevoegen: Tijdens het lasproces wordt een bepaalde hoeveelheid hulpabsorptiemiddel, zoals poeder of vloeistof, aan de las toegevoegd. Deze absorbers absorberen laserenergie en verminderen de reflectiviteit. Het juiste absorptiemiddel moet worden geselecteerd op basis van de specifieke lasmaterialen en toepassingsscenario's. In de lithiumbatterijindustrie is dit onwaarschijnlijk.
3.4 Gebruik optische vezels om laser over te brengen: Indien mogelijk kan optische vezel worden gebruikt om laser naar de laspositie over te brengen om de reflectiviteit te verminderen. Optische vezels kunnen de laserstraal naar het lasgebied leiden om directe blootstelling aan het oppervlak van het lasmateriaal te voorkomen en het optreden van reflecties te verminderen.
3.5 Laserparameters aanpassen: Door parameters zoals laservermogen, brandpuntsafstand en brandpuntsdiameter aan te passen, kan de verdeling van laserenergie worden gecontroleerd en kunnen reflecties worden verminderd. Voor sommige reflecterende materialen kan het verminderen van het laservermogen een effectieve manier zijn om reflecties te verminderen.
3.6 Gebruik een bundelsplitser: Een bundelsplitser kan een deel van de laserenergie naar het absorptieapparaat leiden, waardoor het optreden van reflecties wordt verminderd. Apparaten voor bundelsplitsing bestaan gewoonlijk uit optische componenten en absorbers, en door geschikte componenten te selecteren en de lay-out van het apparaat aan te passen, kan een lager reflectievermogen worden bereikt.
4. Ondersnijding bij lassen
Welke processen veroorzaken bij het productieproces van lithiumbatterijen meer kans op prijsonderbieding? Waarom vindt er onderbieding plaats? Laten we het analyseren.
Ondersnijding, over het algemeen zijn de lasgrondstoffen niet goed met elkaar gecombineerd, de opening is te groot of de groef verschijnt, de diepte en breedte zijn in principe groter dan 0,5 mm, de totale lengte is groter dan 10% van de laslengte, of groter dan de productprocesstandaard de gevraagde lengte.
Bij het hele productieproces van lithiumbatterijen is de kans groter dat er sprake is van onderbieding, en deze wordt over het algemeen verspreid bij het afdichtende voorlassen en lassen van de cilindrische afdekplaat en het afdichtende voorlassen en lassen van de vierkante aluminium afdekplaat. De belangrijkste reden is dat de afdichtende afdekplaat moet samenwerken met de schaal bij het lassen. Het aanpassingsproces tussen de afdichtende afdekplaat en de schaal is gevoelig voor overmatige lasspleten, groeven, instorten, enz., dus het is bijzonder gevoelig voor ondersnijdingen. .
Dus wat veroorzaakt onderbieding?
Als de lassnelheid te hoog is, heeft het vloeibare metaal achter het kleine gaatje dat naar het midden van de las wijst geen tijd om zich opnieuw te verdelen, wat resulteert in stolling en ondersnijding aan beide zijden van de las. Met het oog op de bovenstaande situatie moeten we de lasparameters optimaliseren. Simpel gezegd: het zijn herhaalde experimenten om verschillende parameters te verifiëren en DOE te blijven doen totdat de juiste parameters zijn gevonden.
2. Overmatige lasopeningen, groeven, instortingen enz. van lasmaterialen zullen de hoeveelheid gesmolten metaal die de openingen opvult verminderen, waardoor de kans op ondersnijdingen groter wordt. Dit is een kwestie van apparatuur en grondstoffen. Of de lasgrondstoffen voldoen aan de inkomende materiaalvereisten van ons proces, of de nauwkeurigheid van de apparatuur aan de eisen voldoet, enz. De normale praktijk is om de leveranciers en de mensen die verantwoordelijk zijn voor de apparatuur voortdurend te martelen en te slaan.
3. Als de energie aan het einde van het laserlassen te snel daalt, kan het kleine gaatje instorten, wat plaatselijke ondersnijding tot gevolg heeft. De juiste afstemming van kracht en snelheid kan de vorming van ondersnijdingen effectief voorkomen. Zoals het oude gezegde luidt: herhaal experimenten, verifieer verschillende parameters en ga door met DOE totdat je de juiste parameters hebt gevonden.
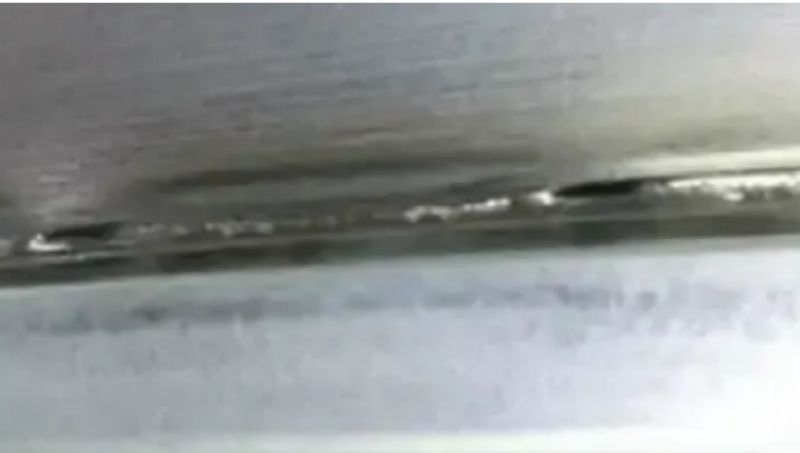
5. Instorten van het lascentrum
Als de lassnelheid laag is, zal het gesmolten bad groter en breder zijn, waardoor de hoeveelheid gesmolten metaal toeneemt. Dit kan het handhaven van de oppervlaktespanning bemoeilijken. Wanneer het gesmolten metaal te zwaar wordt, kan het midden van de las zinken en putten en putten vormen. In dit geval moet de energiedichtheid op passende wijze worden verlaagd om te voorkomen dat het smeltbad instort.
In een andere situatie vormt de lasspleet gewoon een instorting zonder perforatie te veroorzaken. Dit is ongetwijfeld een probleem bij het persen van apparatuur.
Een goed begrip van de defecten die kunnen optreden tijdens het laserlassen en de oorzaken van verschillende defecten maakt een meer gerichte aanpak mogelijk om eventuele abnormale lasproblemen op te lossen.
6. Lasscheuren
De scheuren die ontstaan bij continu laserlassen zijn voornamelijk thermische scheuren, zoals kristalscheuren en liquefactiescheuren. De belangrijkste oorzaak van deze scheuren zijn de grote krimpkrachten die door de las worden gegenereerd voordat deze volledig stolt.
Er zijn ook de volgende redenen voor scheuren bij laserlassen:
1. Onredelijk lasontwerp: Een onjuist ontwerp van de geometrie en de grootte van de las kan lasspanningsconcentratie veroorzaken, waardoor scheuren ontstaan. De oplossing is om het lasontwerp te optimaliseren om lasspanningsconcentratie te voorkomen. U kunt geschikte offsetlassen gebruiken, de lasvorm wijzigen, enz.
2. Verkeerde combinatie van lasparameters: Een onjuiste selectie van lasparameters, zoals een te hoge lassnelheid, een te hoog vermogen, enz., kan leiden tot ongelijkmatige temperatuurveranderingen in het lasgebied, wat resulteert in grote lasspanningen en scheuren. De oplossing is om de lasparameters aan te passen aan het specifieke materiaal en de lasomstandigheden.
3. Slechte voorbereiding van het lasoppervlak: Als het lasoppervlak niet goed wordt gereinigd en voorbehandeld vóór het lassen, zoals het verwijderen van oxiden, vet, enz., zal dit de kwaliteit en sterkte van de las aantasten en gemakkelijk tot scheuren leiden. De oplossing is om het lasoppervlak adequaat te reinigen en voor te behandelen om ervoor te zorgen dat onzuiverheden en verontreinigingen in het lasgebied effectief worden behandeld.
4. Onjuiste controle van de warmte-inbreng bij het lassen: Een slechte controle van de warmte-inbreng tijdens het lassen, zoals een te hoge temperatuur tijdens het lassen, een onjuiste afkoelsnelheid van de laslaag, enz., zal leiden tot veranderingen in de structuur van het lasgebied, wat resulteert in scheuren . De oplossing is om de temperatuur en de koelsnelheid tijdens het lassen te regelen om oververhitting en snelle afkoeling te voorkomen.
5. Onvoldoende spanningsverlichting: Onvoldoende spanningsverlichting na het lassen zal resulteren in onvoldoende spanningsverlichting in het gelaste gebied, wat gemakkelijk tot scheuren zal leiden. De oplossing is om na het lassen de juiste spanningsontlastende behandeling uit te voeren, zoals een warmtebehandeling of trillingsbehandeling (belangrijkste reden).
Wat betreft het productieproces van lithiumbatterijen: welke processen veroorzaken eerder scheuren?
Over het algemeen kunnen scheuren optreden tijdens het afdichtlassen, zoals het afdichtlassen van cilindrische stalen omhulsels of aluminium omhulsels, het afdichtlassen van vierkante aluminium omhulsels, enz. Bovendien is tijdens het moduleverpakkingsproces ook het lassen van de stroomafnemer gevoelig. tot scheuren.
Uiteraard kunnen wij ook lasdraad, voorverwarmen of andere methoden gebruiken om deze scheuren te verminderen of te elimineren.
Posttijd: 01-sep-2023